Optimización de la logística a temperatura controlada
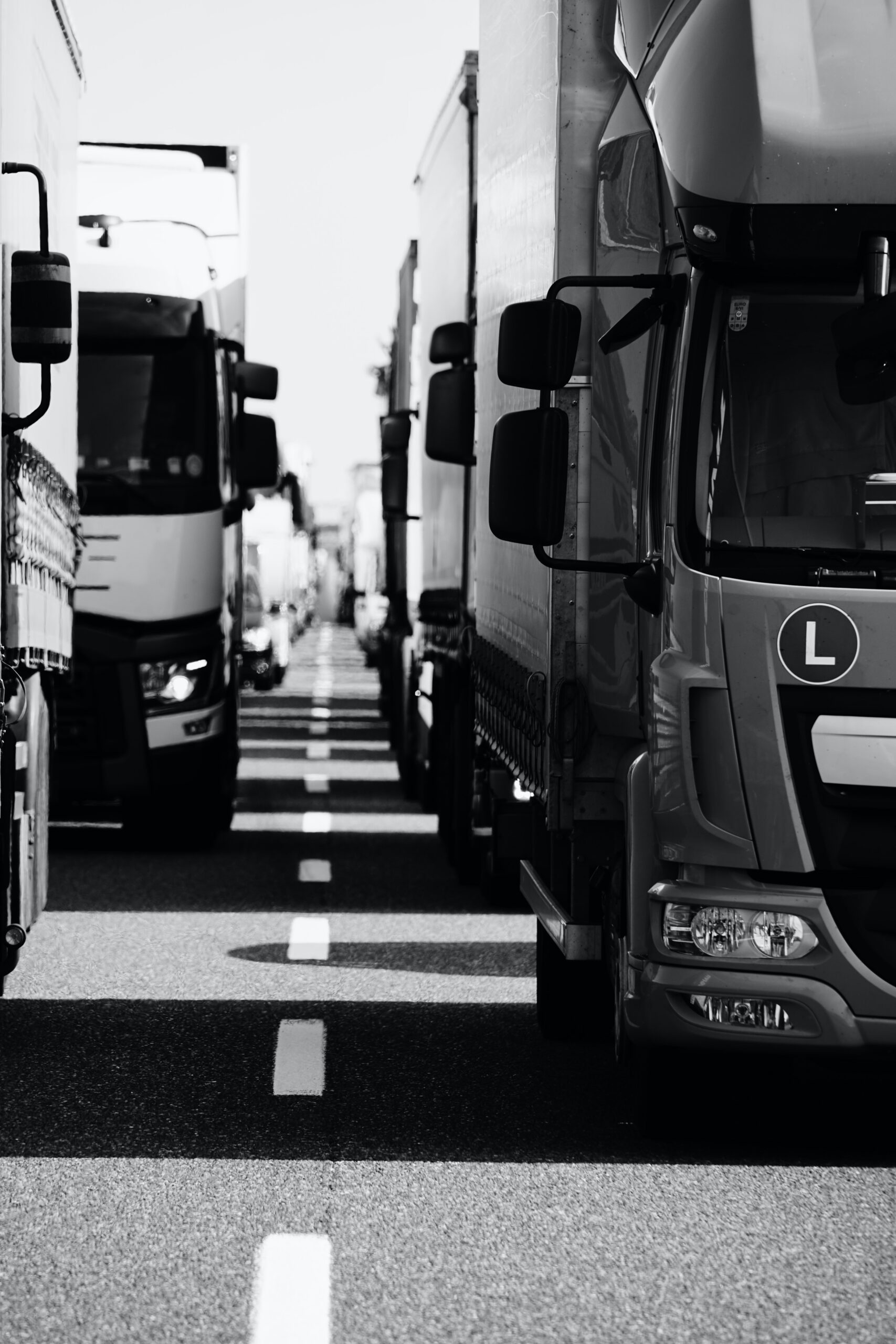
Temperature-controlled logistics is an added challenge to the already complicated distribution of goods. The great challenge is to maintain a controlled, stable and safe temperature throughout the journey from the factory to the final consumer of that merchandise.
As logisticians, we must ensure the security that this product has not been damaged due to an inappropriate temperature, as it surely is.
There are many products that require temperature, from perishables such as food (fruit, vegetables, or any type of fresh food), medicines, or even precision parts that the temperature could modify their shape to give common and not so common examples. Likewise, we can find different temperature levels:
- Without temperature: 15º-40º
- Controlled temperature:
- Refrigerated: 0ºC ←→ 8ºC
- Frozen: 0ºC ←→ -20ºC
- Ultra frozen: Below -40ºC
Products that require controlled temperature are transported by vehicles specially designed to maintain the temperature inside. To do this, they are equipped with powerful cooling systems. Some in the form of an autonomous system with their own diesel engines, others connected to the vehicle itself that provides the energy, or even some are powered by passive cold (incorporating ice charges that preserve the cold).
What challenges do controlling cold in the supply chain entail?
Fuel consumption
Refrigerated vehicles have much higher consumption than conventional vehicles. Refrigeration is a process that consumes a large amount of energy, and that translates into liters of diesel. The greater the temperature difference between the inside of the truck and the outside, the more work the cooling system must do, consuming more in summer.
Therefore, the products should be on the truck for the minimum amount of time possible. Efficient logistics management will try to minimize this loading time.
Another action that generates a great impact on consumption is the opening of doors. Every time a refrigerated truck opens its doors, the outside heat penetrates into the truck, causing consumption to increase. The solution is to minimize the opening of doors, and above all, minimize the time they remain open. Good planning that allows the load to be ordered so that the unloading time is the minimum, will reduce the opening time, reducing consumption.
Route optimization systems that allow efficient route planning, reducing travel time and efficiently organizing vehicle loading are key to reducing consumption, costs and improving service.
Cold chain management and security
Ensuring that merchandise has not undergone heating and refreezing is critical. Many goods could spoil, even becoming dangerous for human consumption. Examples such as fruit that at high temperatures due to its high sugar content can generate the colonization of bacteria that harm the product, or pharmaceutical material such as vaccines or antibiotics that see their effectiveness reduced due to high temperatures.
Active monitoring of products and/or their transportation is key to ensuring that products are transported safely. Dataloggers and all types of temperature control probes are key tools for this type of logistics.
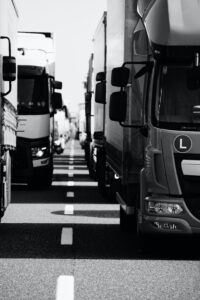
Conclusions
The cold logistics chain has a large number of challenges to face. We have discussed some examples with the main challenges such as logistics optimization to reduce consumption or temperature monitoring to ensure the cold chain at all times. These are some of the main challenges of a key sector for many industries.
At SmartMonkey we help all types of refrigerated transport companies optimize their distribution, save time and fuel in just 24 hours. Try it here.